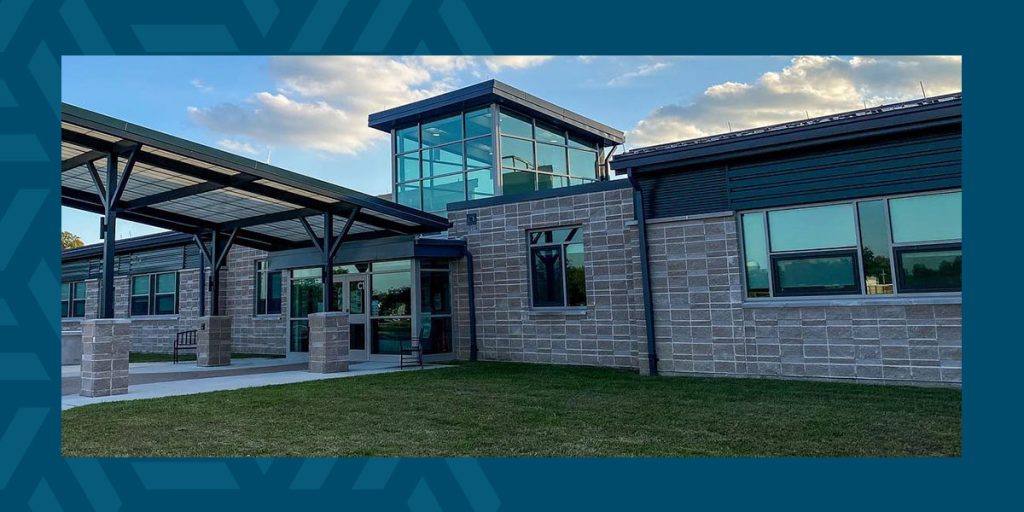
Concrete is inherently porous, meaning it absorbs water easily. In residential and commercial buildings, water and moisture can cause bacteria and mold to accumulate on concrete surfaces.
For instance, exterior walls, basement walls and outdoor walkways are exposed to humidity and rainwater. This makes them vulnerable to mold buildup. Additionally, cracks and crevices in concrete can catch rainwater, creating prime breeding grounds for mold growth.
Therefore, proper moisture control for concrete is a must. Concrete masonry units (CMUs) are more effective for waterproofing than poured concrete. Furthermore, managing condensation and mold buildup in concrete masonry walls is simple with the right tips. Learn how to prevent moisture in concrete walls in this guide.
Why Is It Important to Prevent Mold Growth?
Mold may be essential in nature, as it removes dead organic matter to make room for fresh nutrients. However, it also produces acid that can damage concrete’s structural integrity.
Mold feeds on various particles that get trapped within concrete, such as moisture, bacteria, dirt, pollen and dust. It can gradually deteriorate concrete and render it more porous, allowing more bacteria and water to enter the material.
Additionally, excess mold exposure can pose risks to human health. Mold creates volatile organic compounds. Touching or inhaling it can trigger allergic reactions, upper respiratory distress and other symptoms, particularly in sensitive individuals.
How to Stop Condensation on Concrete Walls
How do you prevent water and condensation from degrading concrete units? From using sealers and coatings to installing dehumidifiers, there are various simple measures you can take to preserve your structure. Here are some tips for controlling moisture and mold in concrete masonry walls.
1. Prioritize Waterproofing in Your Initial Construction Plans
Before constructing the wall, it’s important to integrate waterproofing elements from the start. When reinforced with integral water repellents, CMUs offer effective condensation control, making them a premier choice. Here are some other key considerations as you plan your construction project:
- Water vapor and air retarders: Air barriers and vapor retarders help minimize water retention throughout the structure. They can also increase energy efficiency by diffusing moisture, warming the structure during cold seasons and cooling it during hotter seasons.
- Rainscreens: A rainscreen is an attachment that sits away from the water-resistant barrier of the exterior wall. It forms an air cavity behind the cladding vented at the wall’s top and bottom. Rather than ventilation, it uses a warm cavity with an opening in the bottom. This cavity reduces the chance of water invading the unit.
- Air gaps: An air gap provides a space for condensation to evaporate. However, keep in mind that using mesh or mortar to open the space can clog the cavity and hinder airflow. We recommend a rainscreen drainage plane to implement an air gap. This plane extends from the wall’s weep holes (passages for water to escape the structure) to its highest point.
- Wall structure: Excess airflow can bring in water vapor. That’s why it’s important to balance drying and drainage without encouraging spore growth. Make sure the structure is airtight enough to restrict airflow and vapor. This can help keep moisture and mold growth at bay.
- Site drainage: Water should move away from the structure, not toward it. Proper grading and site drainage help keep water away from the concrete unit. Consider installing permeable pavers around the site.
When you incorporate waterproofing components into the wall from the get-go, you’ll experience fewer and less significant moisture problems later on. Additionally, note and plan for any water sources that could present issues, like:
- Plumbing.
- Rainwater.
- Proximity to an ocean, a river or another body of water.
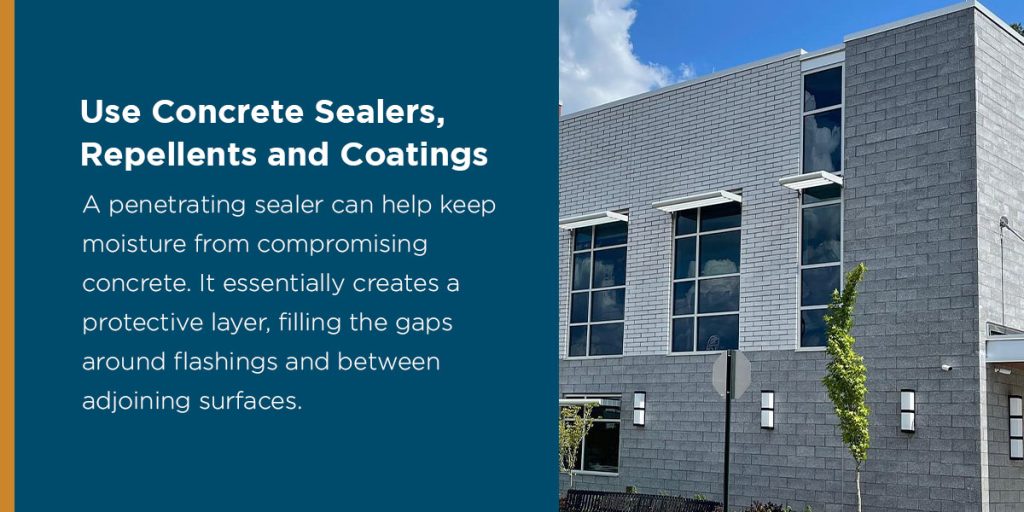
2. Use Concrete Sealers, Repellents and Coatings
A penetrating sealer can help keep moisture from compromising concrete. It essentially creates a protective layer, filling the gaps around flashings and between adjoining surfaces. These gaps would otherwise allow passages for water and moisture to enter the unit.
You can apply water repellents and coatings to the wall’s exterior to minimize moisture entry, prevent degradation and enhance its visual appeal. When applied to CMUs, exterior wall repellents help:
- Prevent moisture buildup.
- Minimize staining from environmental pollutants.
- Enhance color and texture.
Consider starting with a concrete densifier — a liquid chemical that helps fill pores and boost surface density — as a primer. After applying the densifier, use a penetrating concrete sealer.
Types of Water-Repellent Mixtures for CMUs
There are two main classifications of water-repellent mixtures for moisture control:
- Integral water repellents: Concrete block manufacturers apply integral water repellents during production. These substances provide optimal coverage and even distribution. Most of them are polymetric-based and help prevent efflorescence, a crystalline deposit of salts. Efflorescence is notorious for causing moisture issues and damaging building materials like concrete, brick, stucco and stone.
- Surface treatments: While manufacturers usually apply the repellent mixture during CMU production, you can find blocks without this additive. In that case, you can add the mixture to the mortar after curing. Surface treatments are available in various forms, including sprays and paints. You can choose from transparent acrylic or silicone surface treatments, as well as water-based latex paints. Note that cement-based coatings like stucco and mortar can alter texture. Clear surface treatments help boost waterproofing properties without changing the wall’s appearance.
There are also several types of water-repellent materials, like calcium stearate, polymetric and tall oil. Polymetric is usually the repellent of choice to prevent moisture. It yields a stronger bond between the mortar and CMU without compromising aesthetics.
You can paint over the polymetric mixture and still ensure a neat, uniform appearance. Tall oils and calcium stearate tend to increase the mortar’s air content and bond less effectively.
3. Dry Out the Surrounding Area
Moisture harbors mold growth, making dry surfaces ideal for keeping mildew away. If your concrete wall is in a water-prone space, you can dry out the surrounding environment in a few ways:
- Use a low-speed, high-volume fan.
- Turn the heat up and air conditioner down to keep the air and concrete at similar temperatures.
- Use a dehumidifier to decrease condensation and remove moisture from the air.
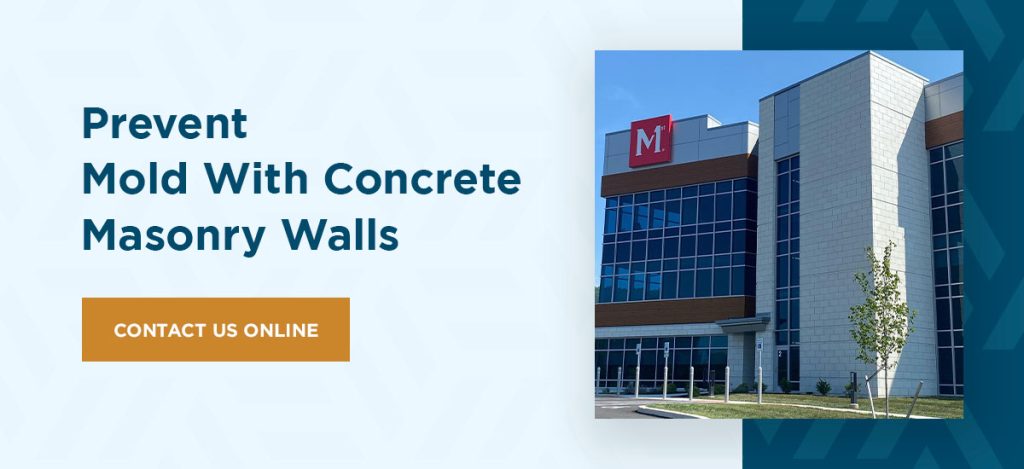
Prevent Mold With Concrete Masonry Walls
At Nitterhouse Masonry, we provide high-quality construction materials designed to preserve the strength and integrity of your concrete structures. We manufacture our durable, eco-friendly architectural concrete blocks with integral water repellents. This careful production process offers optimal defense against moisture and mold spores.
Additionally, our CMUs accommodate various interior and exterior applications. They come in a range of shapes, sizes, colors and styles, making it easy to find solutions for your unique project and architectural requirements.
If you’re looking for high-strength, visually appealing architectural blocks that keep moisture and mold away, turn to Nitterhouse Masonry. Contact us online about getting the right building materials.